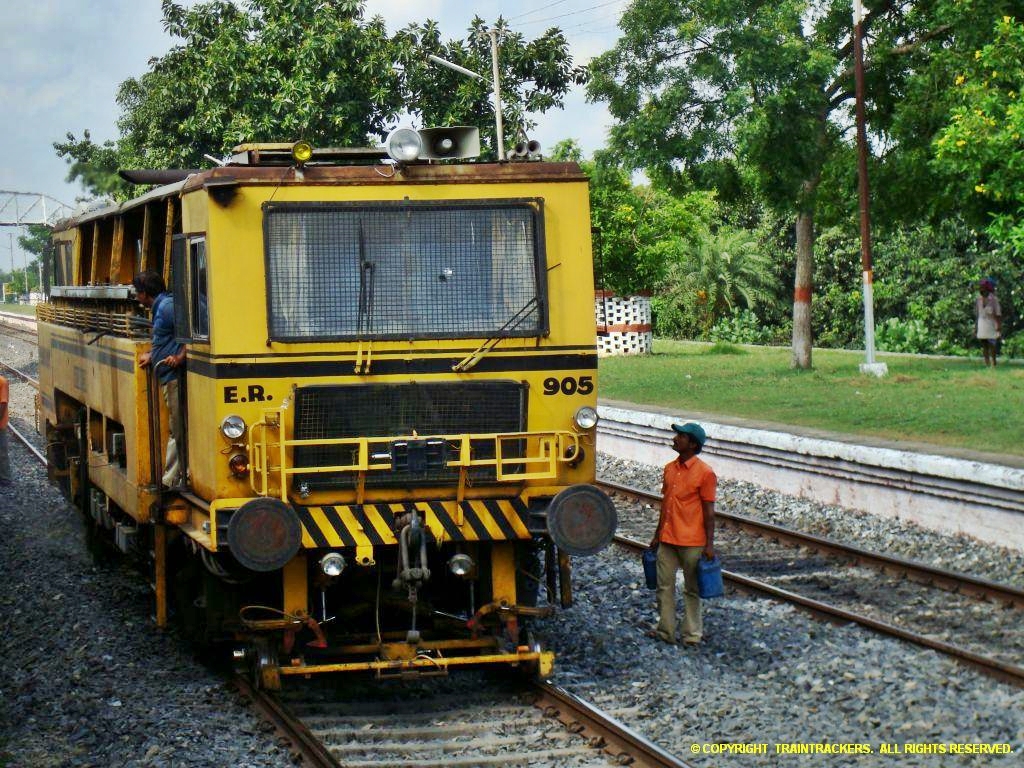
The principle of Continuous Action Leveling, Lining and Tamping machine is based on the notion of separating the main frame from the work unit frame. This means that the main frame can move forward continuously during work, when the essentially cyclic action of the working unit for lifting, lining and tamping is limited to the sub-frame. As a reason the operations lifting, lining and tamping are executed at standstill. The guarantees optimum quality in the restoration of the track geometry. The working speed of these machine lies up to 50% above that of the conventional tamping machine. Even short train intervals can be used effectively and cost-efficiently. Due to the substantially lower acceleration of mass, the wear on breaks as well as on hydraulic and pneumatic components is reduced. Due to the separation of main frame and sub-frame, the vibrations of the work units are not transmitted to the cabins. Working comfort is considerably improved, as the operator is no longer subjected to the acceleration pull and the braking jolts.The continuous working action permits ideal combination with other continuous action machines such as a ballast plough and a dynamic track stabilizer, to form a high capacity mechanized maintenance train.
The machine main frame is made of rolled profiles and steel sheets, produced using the most up-to-date welding methods: the design guarantees stability and precision even on heavy types of permanent way. Two 2-axled bogies ensure smooth vehicle running. The sub-frame carries all work units and measuring systems that use the cyclic work sequence: the lifting and lining units, the two tamping units and the sleeper-end consolidators. At the front it is supported on the main frame via a longitudinal roller guide. The sub-frame axle, powered by hydraulics during working travel, hydraulic cylinders and a pneumatic brake ensure the cyclic work sequence.
The two high-pressure tamping units work according to the well-proven non-synchronous uniform pressure tamping principle. Force equilibrium between the tine pairs, directional vibration in the squeeze direction and the ideal vibration frequency of 35 Hz guarantee completely uniform tamping. For work in curves the unit can be centered automatically over each rail. The above machine in the photo uses two tamping units with 32 tamping tines in all for tamping two sleepers per tamping cycle.
The two well-proven roller lifting and lining units lift and line the track in one operation. The units have a total of four roller-lifting clamps. The distribution of the lifting forces and the exact centering of the units over the rails prevent the occurrence of tilting moments and excessive wear on rail fastenings. At the start of work they are lowered on to the track and remain there during entire work process. Lifting and lining is carried out only when the unit is at standstill. This permits precise lifting and lining. During forward motion the corresponding hydraulic cylinders are switched to pressure less mode.
The cabin at the front of the machine houses the operating controls for the lining and leveling system and is equipped with all necessary controls for transfer travel. In the second cabin all operating and monitoring controls for operations and for transfer travel are clearly laid out.